High-volume wrapping centers benefit most from regular stretch wrap machine repair.
High-volume wrapping centers benefit most from regular stretch wrap machine repair.
Blog Article
A Comprehensive Technique to Dealing With Stretch Cover Equipment Fixing Obstacles
You recognize that stretch wrap equipments are vital for keeping effectiveness in product packaging procedures. Problems can occur that disrupt performance. What are the ideal strategies to ensure your equipments run smoothly?
Recognizing Typical Stretch Wrap Device Issues
When you count on stretch cover equipments for effective packaging, it's crucial to recognize common problems that can interrupt procedures - stretch wrap machine repair. One common problem is inconsistent stress, which can cause poor wrapping and compromised tons stability. If you discover the film isn't sticking properly, check for damaged rollers or incorrect settings
One more problem you could encounter is movie damage, commonly created by incorrect movie kind or device breakdowns. Routinely check the maker for indications of deterioration to avoid this.
In addition, watch on movie build-up or jams, which can stop production. Commonly, this occurs due to imbalance or particles in the device.
Lastly, improper sealing can cause lots splitting up throughout transportation. Ensure your machine is adjusted properly to keep the stability of your plans. By remaining watchful and resolving these problems immediately, you can help with smoother operations.
The Importance of Regular Preventive Upkeep
Routine precautionary upkeep is crucial for maintaining your stretch cover maker running efficiently and successfully. By consistently checking and servicing your tools, you can find prospective issues prior to they escalate right into costly fixings. This proactive strategy not only expands the life expectancy of your machine however likewise ensures that it runs at peak efficiency.
You need to arrange regular inspections to clean, lube, and change used parts. Keeping your machine adjusted aids keep perfect wrapping top quality, reduces waste, and improves productivity. Furthermore, documenting upkeep tasks produces a reputable history that can educate future decisions.
Do not neglect the importance of training your staff on maintenance finest methods. When everybody understands just how to care for the equipment, you lessen the risk of operator error bring about break downs. In other words, committing to regular precautionary upkeep is a clever investment that settles in minimized downtime and improved effectiveness in your operations.
Troubleshooting Methods for Quick Fixes
Reliable troubleshooting methods can substantially decrease downtime when your stretch wrap maker encounters issues. Is the device not covering effectively or is it making uncommon sounds?
Following, inspect the machine's setups and controls; occasionally, an easy modification can settle the concern. Evaluate the movie stress and placement, as improper configuration can cause covering failures. Don't neglect electric links; loose or damaged cables can interfere with functionality.
If you're still dealing with difficulties, consider running analysis examinations if your device has that ability. Paper each action you take, as this can assist in future troubleshooting and repair services. Ultimately, don't think twice to speak with a technician if you can not settle the problem swiftly. Effective fixing keeps your procedures running smoothly and decreases costly hold-ups.
Training Operators for Effective Machine Use
To ensure your stretch cover machine operates at peak efficiency, appropriate training for drivers is necessary. When drivers recognize the equipment's functionalities, they can optimize its prospective and reduce downtime.
Encourage them to exercise under supervision, attending to any type of inquiries or concerns they might have. Regularly scheduled refresher programs can maintain their skills sharp and aid them adjust to any kind of updates or modifications in technology.
Furthermore, infuse a society of responsibility by equipping operators to report concerns or suggest improvements. This positive strategy not just enhances their self-confidence however likewise adds to the total performance of your procedures. With trained operators, you'll see fewer errors and increased productivity, ensuring your stretch wrap equipment stays a valuable property.
Building a Strong Interaction Network In Between Teams
Well-trained drivers can just perform at their finest when there's a strong interaction network between groups. Efficient interaction eliminates misconceptions and warranties everybody's on the exact same web page concerning maker operations and repair service requirements. Urge regular check-ins and meetings to discuss concerns, share insights, and address concerns.
Utilizing modern technology, like messaging applications or joint systems, can boost real-time interaction, making it less complicated to report troubles and share updates swiftly. Appointing clear functions and responsibilities fosters responsibility, permitting team members to get to out to the best individual when concerns occur.
Additionally, producing an open atmosphere where every person feels comfortable sharing feedback can cause cutting-edge remedies. By prioritizing interaction, you're not just enhancing equipment efficiency; you're likewise constructing a cohesive team that collaborates perfectly. This joint spirit ultimately leads to quicker repairs and reduced downtime, benefiting the whole procedure.
Purchasing Quality Substitute Components
When it comes to preserving your stretch cover devices, buying quality replacement components is important for guaranteeing trusted efficiency and decreasing downtime. Affordable options may seem alluring, but they usually bring about more considerable problems down the line, costing you extra in repairs and lost performance. By picking top notch parts, you're not simply dealing with a problem; you're enhancing the total performance of your devices.
In addition, top quality components are generally made to stricter requirements, which means they'll fit better and operate more reliably. This reduces the possibility more info of unexpected failures, allowing your procedures to run smoothly. Furthermore, trustworthy distributors frequently provide service warranties, providing you satisfaction in your financial investment.
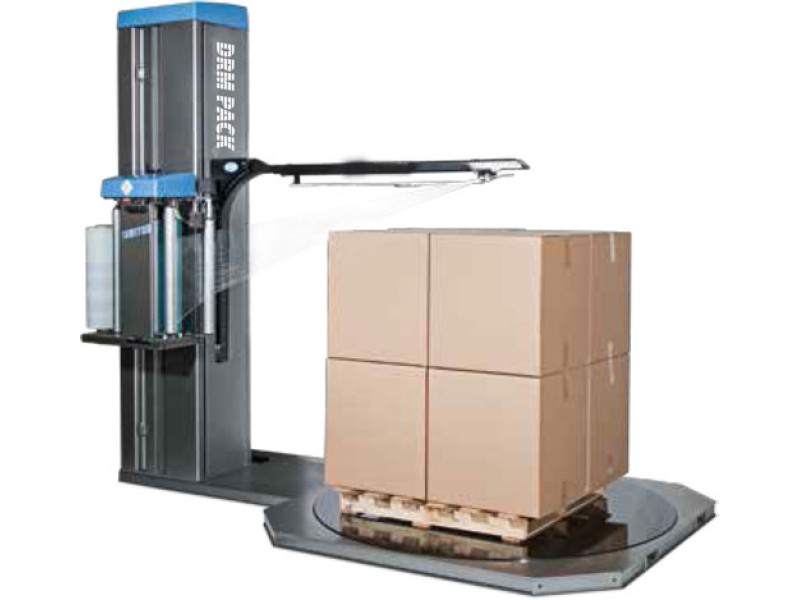
Analyzing Efficiency Information for Constant Enhancement
To improve your stretch wrap equipment's performance, you need effective data collection methods. By examining performance metrics, you can pinpoint locations for enhancement and increase effectiveness. Identifying these possibilities not only enhances operations but likewise lowers downtime and fixing prices.
Information Collection Strategies
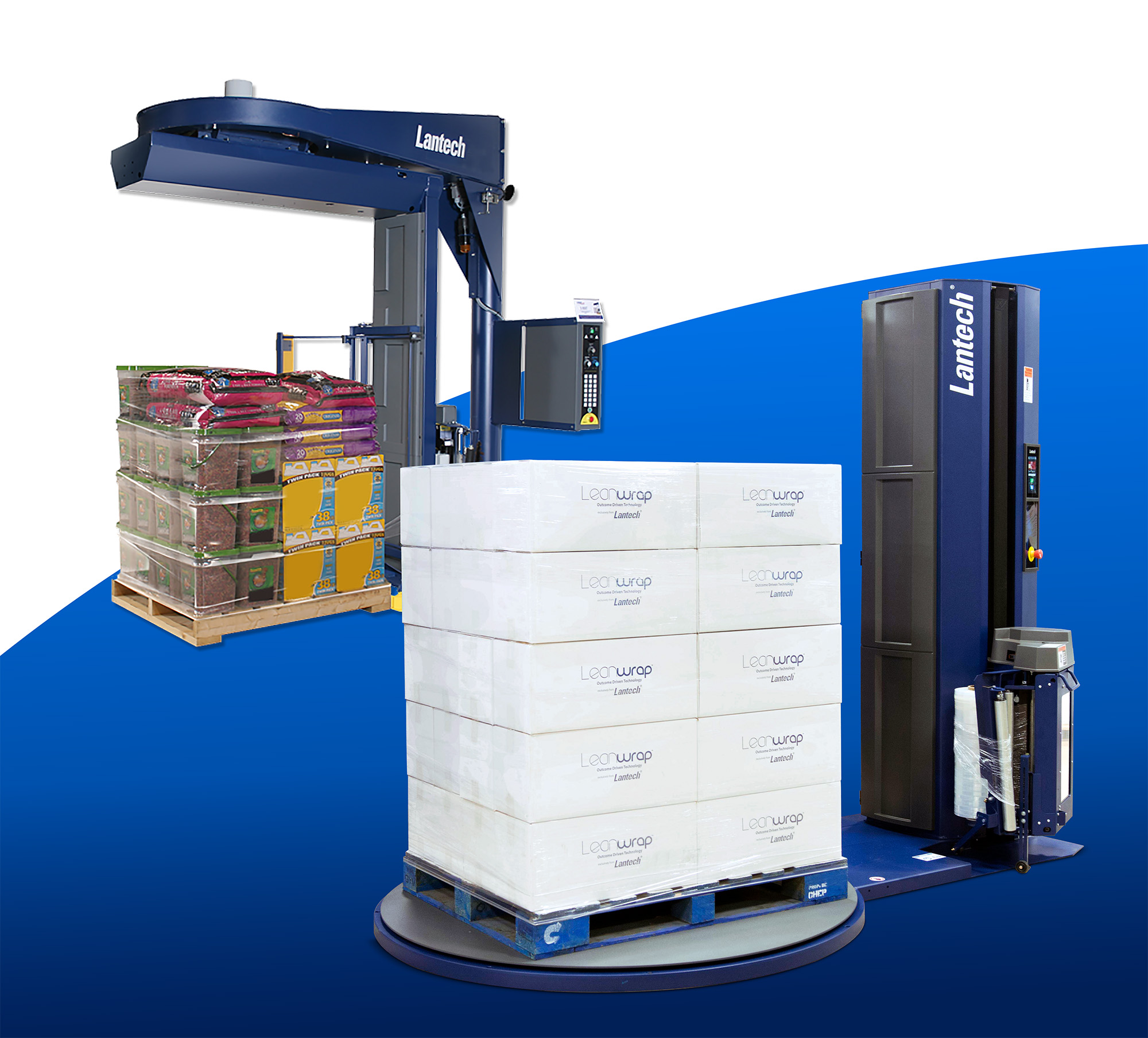
Performance Metrics Examination
While assessing efficiency metrics, it's vital to concentrate on details information points that straight influence your stretch cover equipment's efficiency. Start by tracking cycle times, as they expose how quickly your device operates under typical conditions. Display downtime occurrences to recognize patterns or persisting problems that may require resolving. Watch on movie use, guaranteeing you're not throwing away material, which can influence expenses and efficiency. In addition, assess result high quality by looking for incongruities in the wrapping procedure. By evaluating these metrics on a regular basis, you can identify locations needing interest and take aggressive actions. This constant assessment aids enhance performance, decrease prices, and ultimately enhance your maker's longevity, resulting in an extra reliable covering operation generally.
Identifying Improvement Opportunities
As you analyze efficiency data, you can reveal beneficial improvement possibilities that enhance your stretch cover machine's performance. Look for fads in downtime, cycle times, and wrap quality. By recognizing patterns, you'll see which areas need interest. For example, if frequent breakdowns correlate with specific operating problems, you can adjust procedures to mitigate these problems. Furthermore, compare your information versus market standards to assess your performance. Engage your team in conversations about the findings; their understandings can reveal functional remedies. Implementing minor modifications based upon this analysis can lead to significant gains in efficiency. Frequently reviewing and updating your performance information will assure continuous enhancement, keeping your operations running efficiently and efficiently.
Often Asked Inquiries
Exactly How Can I Inform if My Maker Requirements a Repair Work or Just Maintenance?
To tell if your equipment needs fixing or just upkeep, listen for unusual sounds, check for inconsistent efficiency, and check for noticeable wear. If issues persist after maintenance, it's likely time for a repair.
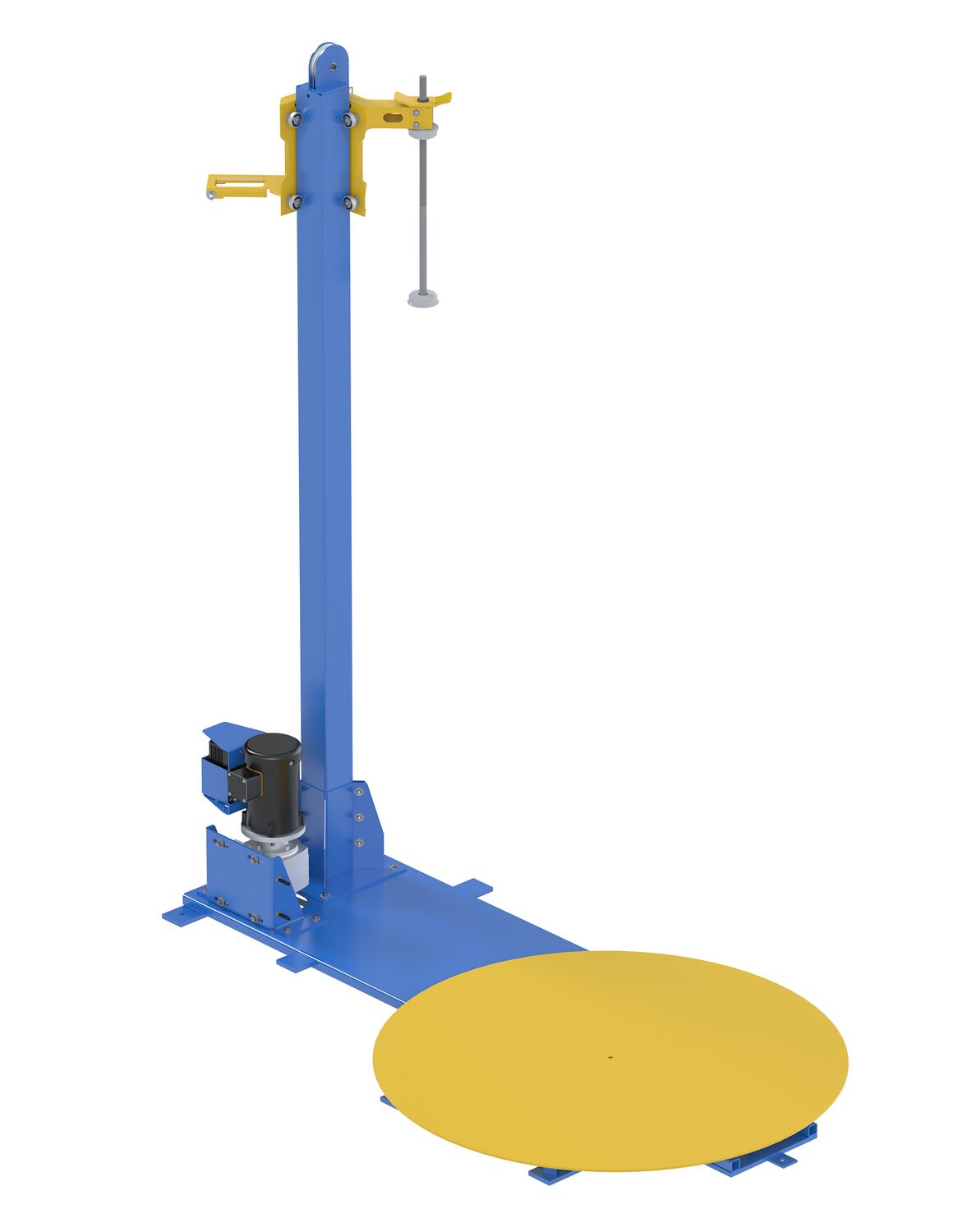
What Is the Average Lifespan of a Stretch Wrap Device?
The average lifespan of a stretch cover equipment is usually five to 10 years, depending on usage and maintenance. Regular care can prolong its life, so maintain an eye on performance and address concerns quickly.
Exist Specific Brand Names Recognized for Better Integrity?
Yes, some brands are understood for their integrity. You'll find that companies like Signode and Lantech usually obtain positive testimonials - stretch wrap machine repair. Looking into individual responses can help you pick a reliable stretch wrap equipment for your demands
What Are the Signs of Poor Operator Training?
If you see frequent errors, inconsistent wrapping, or safety and security cases, those are indicators of bad operator training. Lack of understanding regarding equipment functions or failure to comply with protocols can considerably affect efficiency and security.
Just How Can I Discover a Certified Technician for Repair Works?
To locate a qualified professional for repair services, request for suggestions from industry peers, inspect online evaluations, and verify accreditations. You may also consider contacting regional tools providers who commonly have actually relied on technicians available.
Conclusion
To sum up, dealing with stretch cover device repair service challenges calls for a positive strategy. Do not neglect the relevance of strong communication between teams and continuous examination of equipment result.
Report this page